Transporting Carbon: Steering a Course to a Sustainable Future
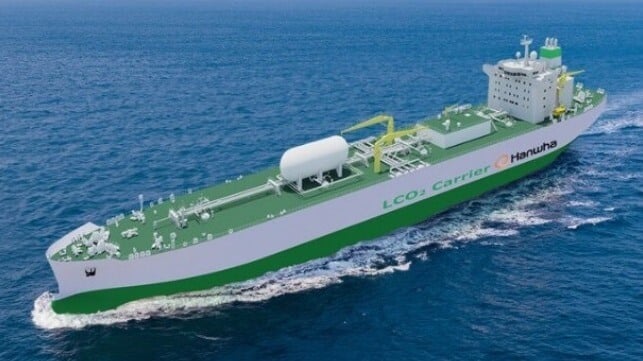
The United States has taken the lead in the international race to capture carbon dioxide (CO2). According to reports, the U.S. will have the capacity to capture 164 million tons of carbon by 2035, which is almost the equivalent of Europe, Canada and the Middle East combined. The global shipping industry remains at the forefront of transporting CO2; however, it is far from plain sailing. In this article, we explore the challenges of CO2 transportation and how the industry can navigate a path forward.
A billion-dollar opportunity
The International Energy Agency (IEA) has heralded carbon capture, utilization, and storage (CCUS) as a key enabler of emission reduction globally, particularly in hard-to-abate industries such as steel, power, chemical, cement and refining. Demonstrating this demand, figures show that carbon capture attracted more than USD 11 billion in global investments in 2023, which is nearly double the level recorded in 2022.
This represents a significant growth opportunity for the global shipping sector, especially for early movers, as the dependence on CO2 shipping carriers and accredited storage tanks is set to increase. Despite opportunities on the horizon, scaling the application on a global level remains a challenge so we are yet to fully understand the possibilities. According to recent analysis, CCUS uptake needs to grow 120 times over by 2050 for all countries to achieve their net zero commitments.
The CCUS market has great potential for growth and development in the U.S., partly due to incentives offered by the government. In 2023, for example, the U.S. Department of Energy announced a $1.7 billion fund for carbon capture demonstration projects, and a $1.2 billion fund for direct air capture (DAC) hubs. This has accelerated many CCUS projects, driving the momentum towards a net zero future. Despite this potential, issues around CO2 transportation persist.
Pipelines vs shipping
For more than 50 years, pipelines on the seabed have been used to transport oil successfully, and this remains an option for CO2 transportation. In our recent whitepaper, CO2 Impurities and LCO2 Carrier Design Practical Considerations, we specified that nearly 360,000 km of pipelines may be required to transport the CO2 captured from industrial processes by 2050.
Since many pipelines are still required for use in the oil and gas industry, they alone won’t meet demand. In fact, the U.S. will need to construct additional CO2 pipelines of between 17,700 and 37,000 km before 2050.
Furthermore, terminal facilities will need to be built which connect land to subsea pipelines or to ships. Subsea pipeline and termination manifolds, as well as riser connections to fixed or floating offshore platforms, are already being studied as viable options with trials underway.
When it comes to transporting CO2 in pipelines, there are many considerations. The CO2 must be set at a supercritical pressure of 73.8 bar and temperature of 31.1° C. In addition to constructing the pipelines at the required temperature and pressure characteristics, materials that avoid corrosion, pitting or cracking will need to be used when considering the content of the CO2 stream (e.g., accompanying water, nitrogen, hydrocarbons, oxygen, sulfur, and sulfides).
Although the use of pipelines in the energy sector is well established, they require a continuous flow of compressed gas, and their user costs are highly dependent on distance. Therefore, the shipping industry is increasingly being looked at as the most viable solution for safely transporting CO2, particularly when in low volumes.
In fact, transporting CO2 by ship has been labeled essential by the European Commission’s EU Taxonomy for Sustainable Activities, as well as the EU Emissions Reading System (EU ETS).
While transporting CO2 in pipelines requires supercritical conditions to be met, shipping it is simpler as it can be in liquefied form (LCO?). This means it can be shipped at varying temperatures and pressures, and a ship can take approximately 1/500th of the volume of CO? transported in pipeline alternatives.
The existing fleet in operation that meets the criteria for LCO2 transportation is limited to only four carriers. They are currently serving the food and beverage industry at small capacities (~1,700 tons CO2), and operating pressures in the range of 15-19 bara (absolute pressure). There are currently two ships that can transport CO2 in the pressure range of 13-18 barg (gauge pressure).
The possibility of transporting CO2 in cryogenic conditions is being analyzed; however, currently, no ship can transport CO2 in the pressure range of 6-8 barg. Interestingly, joint industry projects, like the one between ECOLOG, Hanwha Ocean, Babcock LGE, and the American Bureau of Shipping, are exploring this as a workable solution. Through the project, approval in principle has been issued for a low-pressure, 40,000 cbm LCO2 carrier.
The trials and tribulations of shipping CO2
Unlike onshore CO2 handling systems and transportation by pipelines, there is a lack of engineering data available on shipping CO2. This creates many challenges.
The demand for robust shipping infrastructure to allow the CCUS industry to mature, creates significant economic potential for the shipping industry, while supporting net-zero targets. However, companies need to be aware that to capitalize on the opportunity, they need to invest and build dedicated LCO? carriers to support the transportation of extensive volumes of CO2 captured.
Currently, there are no standards for shipping CO2 with impurities as cargo, only recommendations such as ABS’ guide on liquefied carbon dioxide carriers. For shipping companies, following guides like these can help mitigate health and safety risks. Additionally, corrosion reactions could potentially impact the integrity of the ship and /or create harm to personnel. If liquid CO2 contains more water than gaseous CO2, it can become more corrosive.
Also, a high level of non-condensable impurities can substantially consume the volumetric capacity. For example, the presence of 10 percent hydrogen can reduce the capacity by 27 percent, which would incur a financial loss.
The density of the cargo must also be considered in that lower-density LCO2 reduces a ship’s volumetric efficiency, and a higher pressure limits tank size and increases the wall thickness. The physical properties and transport conditions of CO2 - and consequent issues like compression liquefaction system and power demand - need to be better understood in order to create definitive guidelines for cargo handling and shipping.
The design of the cargo tanks should be in accordance with the International Code for the Construction and Equipment of Ships Carrying Liquefied Gases in Bulk, or IGC code. This code has been the basis for the design of cargo tanks for liquefied petroleum gas (LPG) since the 1960s.
Trials around carrier materials are also underway. New high-strength carbon-manganese steel materials are being developed by steel mills for example that could be used as CO2 Carrier tank material subject to approval by the ship’s Classification Society. Trials like these are critical in that they provide more clarity around ideal pressure, temperature, and composition mechanisms so that we can create the right condition for transporting CO2 in liquid form, throughout the shipping transport chain.
The CCUS industry is gathering pace, allowing many nations to unlock the possibilities of sustainable emissions reduction. However, the transportation of CO2 must be optimized in a way that takes into account human life, environmental protections, cost, and energy demand. If the industry, regulatory bodies, and government continue to collaborate on suitable CO2 applications internationally, the CCUS market will be able to thrive and support the transition to a net zero future.
Dimitrios Bardakos is the Global Carbon Leader at ABS. He is a seasoned professional with over 18 years of experience in corporate strategy and chemical process engineering.
He came to ABS from the onshore industry and a group of companies operating one of Europe's most complex oil refineries. His experience spans corporate strategy and planning; energy transition; refinery operations and economics; process design; engineering, procurement, and construction projects; and health, safety and environment activities.
He graduated from the National Technical University of Athens with a Master of Chemical Engineering, from the University of Piraeus with a Master of Science in Logistics and Supply Chain Management, and the Alba Graduate Business School with Master of Science in Finance.
The opinions expressed herein are the author's and not necessarily those of The Maritime Executive.