Underwater Work in Singapore
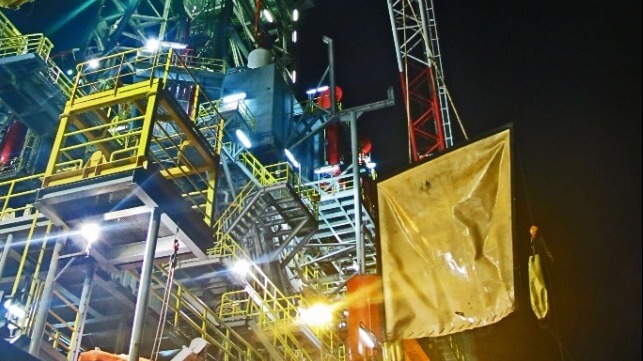
[By: Hydrex]
Hydrex has been performing underwater maintenance and repair operations in Singapore for 40 years. Thanks to their well-stocked local support base they can mobilize to the location very quickly to assist ship owners with any problem they might encounter with the underwater part of their ships.
Singapore has always been a very important port strategically. It is the world's second biggest port, both in size and total shipping tonnage. Most ships passing between the Indian Ocean and the Pacific Ocean go through the Singapore Strait. This makes it the ideal location for vessels to have underwater repair or maintenance work carried out.
Since Hydrex was founded 50 years ago, the company has always strived to find ways of performing operations while cargo operations continue. This allows ships to keep their busy schedule with no or only very minimal delay.
To offer this same service around the world, Hydrex has built strong relationships with high quality local support bases that have the needed material ready for immediate use. Singapore is no exception to this.
For 40 years they have been delivering the well-known Hydrex high quality to ships making a port call in Singapore. This is illustrated by the selection of case studies in this article, some very recent, some from years ago, but all with the same result: a satisfied customer.
Emergency operation on drilling vessel
In 2010 Hydrex sent a team to Singapore to perform an emergency operation on a 154-meter drilling vessel that had just been to drydock for repairs but soon after leaving was still experiencing problems with one of its three bow thrusters.
The owner needed to know the exact reason for the problem as soon as possible so that he could decide whether to redock the vessel before it left for its working location with a view to minimizing off-hire time.
Thanks to the Hydrexfast response center, within 24 hours after they were contacted, a team of 6 diver/technicians was on its way to Singapore. Simultaneously preparations were made by the local support base so that the team could start the operation immediately after it arrived at the vessel’s location. This was only days after the call came in.
The first step was the installation of the unique Hydrex flexible mobdocks. These close off the thruster tunnel and allow for the creation of a dry working environment around the affected bow thruster unit. The cover of the gearbox was then removed and a detailed inspection of the entire unit was carried out. This revealed that both the oil distribution box and the shaft were damaged and that the shaft needed to be replaced in its entirety. The delivery period for a new shaft ruled out a fast in-situ repair and therefore, in consultation with all parties involved, it was decided that a repair in drydock was the best option.
The operation was supervised from inside the monitoring station, located on a work pontoon next to the vessel, by the Hydrex team leader together with a representative of the manufacturer. The owner was able to make an informed decision about whether to drydock his vessel again or not and to make sure that it was in good working order before it left for its working location.
Underwater bilge keel repair
Last June a team of diver/welders was mobilized to Singapore for a crack repair on a 360-meter bulker.
After arriving on site, the team first performed an on-board and underwater inspection of the damaged area. This revealed a crack measuring 232 mm just behind the start of the landing plate of the bilge keel section.
There was a high current where the vessel was anchored. As a result there was little diving time available to work in. The divers could only work during slack tide before the current became too much to allow diving operations.
In close communication with the customer, it was decided to save time by grinding out the crack and rewelding it instead of installing a new insert.
The bilge keel and landing plate were then partially cropped to allow for the installation of a cofferdam on the outside of the hull over the damage. The team could then work on the crack inside the ballast tank without water ingress. The crack was ground out over its entire length and filled with our class approved full penetration welding.
Next the cofferdam was removed and the bilge keel was further adapted to the correct shape. The cropped landing plate was fully welded and closed again.
Installation of new pipe
Last month Hydrex attended a 228-meter drill ship at anchorage in Singapore for the installation of the stub piece for a new overboard pipeline.
After a safety meeting on board the ship and a toolbox meeting with all parties involved, the divers/technicians marked the position of the new insert on the hull. They then drilled a hole in the shell plating to show the location from the inside. A temporary plug was then inserted, and a cofferdam was installed over the area.
The next step was to remove the shell plating where the pipe was going to be installed. Once this was done the pipe could be fitted in the opening. Hydrex certified welders then secured it with full penetration welding which was approved by an independent inspector. The operation ended with the removal of the cofferdam.
New generation propeller repair equipment used for cropping
For another example of an earlier operation we go back to 2015 when Hydrex divers performed a propeller blade repair on a 300-meter container vessel in Singapore. All six blades of the vessel’s propeller were severely damaged and cropping was the only option.
This kind of repair is carried out with propeller blade cutting equipment developed by the company’s research department. In cases where there is an even number of blades, an identical piece will be cropped from the opposite blade to restore the hydrodynamic stability of the propeller. By doing so, the best possible efficiency is obtained.
Because the ship could be trimmed enough to bring the blades above water, scaffolding was installed around the propeller. This allowed the team to perform the operation in the dry.
When the cropping was complete, the blades were polished to minimize any remaining loss of efficiency. The success of the operation was confirmed by the customer. After the operation the vessel completed sea trials and “managed to increase RPM up to 93 and developed 21 knots,” said Maxim Bolduev, Deputy Fleet Manager Southern Shipmanagement. “Before propeller trimming we got 53 RPM and only 14 knots.”
Conclusion
Whenever a shipowner asks Hydrex for assistance in Singapore, they only have to fly in their divers. All logistics for the repair are arranged by the technical department in close cooperation with the local support base. As a result, when the team arrives on site they can immediately start the operation. Because Hydrex is in constant communication with all parties involved, this is usually right after the ship reaches its lay-by berth or anchoring location.
The products and services herein described in this press release are not endorsed by The Maritime Executive.