Re-evaluating Gas Turbine Engines for Future Maritime Propulsion
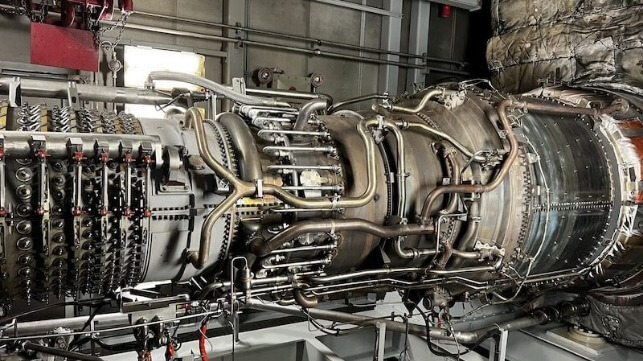
The combination of advances in engine management technology, in the design of heat exchange technology and the chemistry of high-temperature ceramic materials and compounds provide the basis of enhancing the efficiency and market competitiveness of open-cycle and closed-cycle gas turbine engines, including in ship propulsion.
Introduction:
Traditional open-cycle gas turbine engines flow atmospheric air through a compressor, combustion chamber and power turbine. Peak fuel efficiency occurs when operating at maximum power output while the turbine spins at maximum RPM and maximum combustion temperature. Engine efficiency decreases as power output decreases, with half the efficiency available at 25%of output for a single-shaft engine. Externally-heated closed-cycle engines continuously recirculate the same gas through compressors and turbine can deliver high efficiency at 25% of power output. However, the materials of which heat exchangers were made incurred temperature restrictions that restricted both peak efficiency and peak power output.
The complex-cycle gas turbine engine was an open-cycle, triple-shaft engine that combined 2-compressors with 3-turbines, 2-combustion chambers and 2-heat exchangers. Both high-pressure turbine and power turbine spun on separate shafts and had their own combustion chamber. During an earlier era, it was difficult to accurately control air-fuel ratios manually for each combustion chamber that operated in series, upstream and downstream of each other. As a result, in real world operation the complex-cycle gas turbine rarely delivered peak efficiency over a range of power output. However, modern technology offers possibility to both the complex-cycle and closed-cycle gas turbine engines.
Modern advances:
Modern reciprocating internal combustion engines operate with such technology as mass-flow rate sensors, air-fuel ratio sensors, air temperature sensors and computer managed fuel injection that have greatly improved fuel efficiency. There is theoretical potential to adapt such technology to the old classical complex-cycle gas turbine engine, along with the possibility of introducing new generation heat exchanger technology that operates at much higher effectiveness that earlier generation technology. Modern annular counter-flow heat exchangers developed by Ed Proeschel offer heat transfer effectiveness of over 90% compared to 80% for earlier generation counter-flow heat exchangers.
The annular counter-flow heat exchanger can be adapted for operation in both open-cycle and closed-cycle gas turbine engines. Modern turbine blades made from ceramic material retains mechanical properties at 1400-degrees C or 2550-degrees F and allow combustion temperatures of 1200-degrees C without need to cool the turbine blades. While earlier generation heat exchangers were made from steel or stainless steel, there is evolving possibility of being able to make future heat exchangers from materials such as aluminum-nitride and high-purity boron-arsenide that offer higher coefficients of thermal conductivity than that of steel, at much higher temperatures.
Upgraded Complex-Cycle Engine:
An upgraded complex-cycle gas turbine engine would include annular counter-flow heat exchangers installed downstream of both the low-pressure and high-pressure compressors, with computer-controlled fuel injection into combustion chambers placed upstream of both the high-pressure as well as power output turbine. The high-pressure turbine would operate on computer-controlled ultra-lean burn air-fuel ratio to assure sufficient oxygen in its exhaust gas to assure additional combustion to sustain operation of the power output turbine. Sensors connected to the computer would continuously monitor properties of gases flowing from the high-pressure turbine, to assure optimal overall engine performance.
The power output of a future computer-monitored and computer-controlled complex-cycle gas turbine could rival that of the largest maritime diesel engines rated at over 100,000-horsepower and up to 50% thermal efficiency. To assure optimal turbine engine efficiency in cargo ship propulsion, the power output turbine could drive a variable pitch marine propeller via a planetary reduction gear system. While an optional electrical power transmission between power turbine and propeller would incur a reduction in overall engine efficiency, such a layout would be suitable for passenger cruise ship operation.
Bottom-cycle Steam Engine:
The complex-cycle gas turbine engine has 2-sources of reject heat to assist in the operation of a steam engine, preheating water flowing from the water pump to the boiler. Reject heat from the inter-cooler for the low-pressure compressor would provide primary preheating while turbine engine exhaust gas would provide a secondary source of heat that would further raise water temperature. Combustion of liquid or gaseous fuel would convert the preheated water to steam to operate a steam turbine engine at the equivalent of an elevated level of efficiency.
If a gas turbine engine of 100,000-horsepower operates at near 50% thermal efficiency, its inter-cooler and exhaust would release the equivalent of 100,000-horsepower of thermal energy to preheat water to operate a bottom-cycle steam engine. A combined-cycle engine could operate at the equivalent of between 60% and 70% overall thermal efficiency on either liquid or gaseous fuel. The open-cycle turbine engine offers greater flexibility than a reciprocating engine, in the variety of competitively-priced fuel that could sustain its operation. Higher overall thermal efficiency combined with lower fuel cost enhances the engine’s marketability.
Closed-Cycle Engine:
Externally-heated closed-cycle cycle gas turbine engines continuously recirculate the working gas by cooling it after leaving the power turbine. It replaces the combustion chambers of open-cycle engines with high-temperature heat exchangers, with low-pressure and high-pressure compressors and turbines rotating on a common shaft that drives either an electrical generator or reduction gearbox. Closed-cycle engines can be designed to operate with wide variation in the mass of gas that recirculates within the closed system. Such operation maintains high efficiency over a range of power output as turbines spin at maximum design RPM, with gas entering turbine at maximum temperature.
A closed-cycle engine that delivers 40,000-horsepower with mean-average internal system pressure at 5-times atmospheric pressure (5-ATM) would deliver 8,000-horsepower at comparable thermal efficiency with mean system pressure reduced to 1-ATM. During operation, some exhaust heat will be reintroduced into the engine downstream of the high-pressure compressor. The combination of heat rejected from the low-pressure compressor inter-cooler and residual exhaust heat would partially sustain the operation of a bottom-cycle steam engine. Future development of high-temperature heat exchangers made from compounds such as highly-purified boron arsenide with high thermal conductivity promise to assure engine efficiency.
Stored Thermal Energy:
Solar thermal power stations use stored thermal energy to generate several hours of electric power after sunset. The thermal storage medium is low-cost salt compounds of sodium and potassium that melt at sufficiently high temperature to generate steam. Advances in high-temperature ceramic chemistry have produced corrosion-resistant compounds that maintain constant mechanical properties up to 1400-degrees C (2550 F). Open-cycle gas turbine engines require heated air or gas to enter the power turbine at temperatures to 1200-degrees C, while single-shaft, closed-cycle turbines with single compressor and single turbine can operate with air heated to 900-degrees C.
Sodium fluoride (NaF) that historically was a waste byproduct of the aluminum smelting industry, melts at just under 1,000-degrees C (1800 F) with heat-of-fusion of 300-BTU/pound. The aluminum industry mixes the mineral cryolite (Na3AlF6) from Iceland and Greenland with bauxite (Al2O3) to produce aluminum. A mixture of aluminum oxide (Al2O3) and cryolite can melt at under 1200-degrees C (2,200 F) with heat-of-fusion at some 400-BTU/pound, with usable life expectancy of 1-million deep-drain cycles. Future research offers the possibility of closed-cycle gas turbine engines operating from stored thermal energy in both stationary land-based applications and in future maritime propulsion.
Thermal Recharge:
Much advancement has occurred over the past decade in the development of micro and mini-nuclear power conversion. One future possibility would involve a micro or mini-reactor being brought to quayside on a railway carriage, then transferred on board a ship for the purpose of replenishing the onboard thermal storage supply that would sustain ship propulsion for several hundred nautical miles. A fleet of ships assigned to short-sea shipping service could operate between ports located within the operating range of each ship, allowing a small number of micro or mini reactors to sustain the operation of a fleet of ships.
Conclusions:
A 3-shaft open-cycle gas turbine engine using modern electronic engine management technology installed in duplicate or even triplicate, would operate efficiently and reliably over a wide range of power output, even for extended duration cycles. Likewise, a single-shaft closed-cycle gas turbine engine using modern and evolving ceramic-based, annular configuration heat-exchange technology could operate at competitive levels of efficiency using a wide range of fuels, including stored thermal energy. The exhaust heat of both types of engines would sustain the operation of a bottom-cycle steam engine, allowing the combined-cycle engine to deliver very competitive levels of thermal efficiency.
While reciprocating marine engines require massive volumes of lubricating oil, turbine engines require a fraction of the amount of lubricant to assure proper operation of engine bearings. Turbine engines also avoid the problem of internal friction and engine wear caused by piston rings sliding on cylinder walls, thereby extending usable service life. While turbine engines are compact, the heat exchangers attached to them will occupy a substantial amount of volume, which would likely be available inside the hull of a ship. The combination of gas turbine engine with steam bottom-cycle engine represents a future propulsion option for large ships.
The opinions expressed herein are the author's and not necessarily those of The Maritime Executive.