Industry Collaboration: Sheer strength
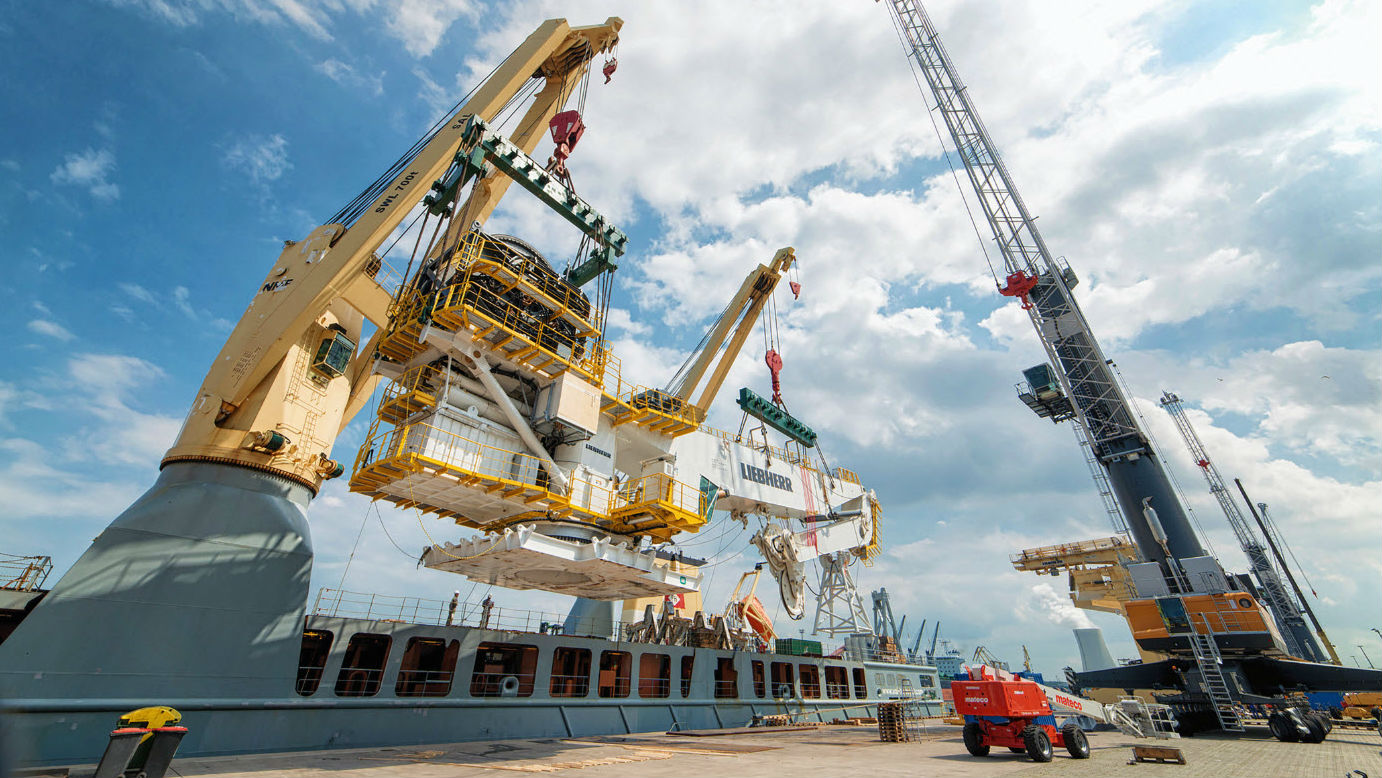
The equipment used to tap offshore energy resources is getting bigger and bigger. Specialized ships are needed to move these huge loads, and close collaboration between the customer, shipping company and classification society is essential.
From the energy sector to industrial machinery and to floating cargo, the technology used in many markets today is getting ever more sophisticated, and the components bigger and heavier. While wind turbine rotor blades rarely reached the 50-metre limit just a few years ago, they average nearly 75 meters today.
Installation of offshore equipment is especially demanding. Around the world engineers are busy developing new concepts for relocationg power generation offshore. Specific plans for mega-installations have emerged in Japan, Belgium and Germany. Offshore Yorkshire, the “Dogger Bank Creyke Beck”, the world’s biggest offshore wind power project to date, will comprise two wind farms of 200 wind turbines each. When completed the project will have a rated capacity of roughly eight billion kilowatt hours per annum, enough for about 1.8 million households.
Today’s maritime equipment, such as mobile, rail-mounted and stationary cranes and stacking equipment used in logistics at sea and inland waterway ports, continues to grow in size and power. For example, in Bronka, the deep-water port of St Petersburg, the biggest mobile in-port crane ever built is about to be commissioned. The LHM 800 series, built by Liebherr, Rostock, has a 308-tonne lifting capacity and a reach of up to 64 meters, enabling it to unload ships that are 22 container bays wide.
“Projects of these dimensions can only be carried out with specialized ships custom-built for oversized, ultra-heavy pieces of cargo,” says Jan Rüde, Ship Type Expert Ship Structures and Outfitting at DNV GL. One of the leading global shipowners in this segment is SAL Heavy Lift, a company of the Japanese K Line Group. With a fleet of 16 heavy-lift cargo ships and a professional engineering department, this Hamburg-based company has earned an excellent reputation across the industry.
Tricky cargo
“Heavy-lift cranes play a key role in the offshore world today and will continue to do so. We have therefore developed a comprehensive heavy-lift crane portfolio with capacities ranging up to 2,000 tons,” says Alexander Gerbert, Offshore Crane Project Administrator at Liebherr-MCCtec Rostock GmbH, a unit of Liebherr’s maritime division.
Liebherr often cooperates with SAL to ship heavy-lift cargo overseas. Recently the two companies moved the RL-K 7500 crane from Rostock to South Korea. The biggest deep-water crane ever developed and built by Liebherr, the RL-K 7500, weighing in at roughly 700 tons, has a 50-metre main boom and can lift loads in waters up to 3,660 meters deep.
Liebherr also entrusted SAL with the transport of two knuckleboom cranes (KBC) for installation ships, as well as two mobile container cranes for a refrigeration ship to South Korea. “It is not only the sheer weight and volume of the cranes that makes this a real challenge,” says shipmaster Matthias Pfeiffer of Trina. “In the case of the KBC cranes we also needed special rigging to protect the main hydraulic cylinders of the cranes against lateral stresses.”
The 160-metre vessel selected for the Liebherr project has three rotary cranes (2 x 700 tons SWL plus 1 x 350 ton SWL). The Liebherr cranes, which had to be shipped fully assembled, first had to be lifted up on land to be mounted inside a stable transport rig to absorb the acceleration forces acting upon the cargo during a sea voyage.
Contrary to other shipping companies which have the cargo loading procedure directed by a port captain, SAL customarily entrusts this task to the ship’s crew. The crew executes the procedure independently as planned by the company’s engineering department. “This enables us to react flexibly in case of an unforeseen event,” explains Captain Pfeiffer.
In the Liebherr project the SAL crew found a way to place the two fully assembled cranes side by side on the same ship. “Transporting the cranes individually would not have been economically feasible for the customer, and disassembling them for shipping would have been too expensive and time-consuming,” says Pfeiffer.
One-size-fits-all is history
When the cargo is loaded onto a ship, this marks the end of a long logistical journey. Shipping damage or a delayed vessel would have severe consequences. For successful shipment it is therefore essential for the customer, the shipping company and the classification society to cooperate very closely.
In the Liebherr and SAL transport project, DNV GL joined in as the third partner. DNV GL has classed nearly half of all heavy-lift vessels worldwide, more than any other classification society. “Every heavy-lift transport is a unique project,” says DNV GL expert Rüde. There are no standardized size categories or one-size-fits-all solutions. Every ship, be it converted or newly built, must be planned and classified individually.
Smaller, older vessels must be retrofitted, while newbuilds must anticipate tomorrow’s requirements. Shipping companies facing such a decision should therefore contact their classification society at the earliest time possible. “Our services go far beyond mere classification. We support our customers from the initial idea to the planning stage through to completion and acceptance of the ship,” says Rüde.
The DNV GL expert continues that there are three main objectives to bear in mind: “Increasing flexibility for transport projects, reducing the costs, and minimizing the risks.” A number of services are combined to address these goals. “At the beginning we sit down with our customer to conduct a thorough requirements analysis: What routes will the vessel serve? What ports will it call at? What is its draught going to be? What type of cargo will it carry? Along these lines we create a realistic, detailed profile for the ship,” says Rüde. Thanks to its AIS database, DNV GL has an enormous information advantage enabling it to give its customers precise recommendations.
There is always potential for optimization. “To give an example, what would be the benefit of designing a vessel for a high maximum speed if it will travel in sea areas where the actual speed is much lower?” Rüde asks. Keeping questions like this in mind, DNV GL presents detailed design concepts for the hull, propeller, rudder, etc. to the customer. The ship’s resistance in water can be determined using CFD simulation. The result is an underwater hull optimized for the customer’s operational profile, ensuring fuel efficiency.
The most important criteria for minimizing risks are the ship’s structural integrity and stability. As cargo gets bigger, longer cargo holds must be designed accordingly – another point the shipbuilding engineers must account for using route data, expected wave conditions, acceleration and other parameters. 3D analyses of the vessel’s steel structure deliver valuable insight into its properties, including the deformation behavior of the hull.
“A detailed analysis of the ship and its cranes with respect to the envisioned cargo cases ensures smooth operation and avoids damage during transit, loading and unloading operations,” Rüde points out. What is more, DNV GL will also determine whether investing in an LNG propulsion option will make economic sense. “This primarily depends on whether the ship will be deployed in ECA zones,” says Rüde.
Another part of the DNV GL services is an accurate calculation of all loading conditions. A set of standardized loading conditions for this ship type will be included with the applicable DNV GL rules effective 1 January. “This will improve transparency by telling shipowners what loading conditions a multipurpose vessel should be designed for to ensure the greatest operational flexibility possible,” Rüde explains. Whatever the case, in addition to the classification services the customer can always choose from a comprehensive set of optional advisory services.
Seamless customer service
As many as three years may pass between the first meeting and the time the keel is laid down. But from the first day each customer is assigned a personal contact at DNV GL with full expertise regarding the specific challenges associated with the ship type. Following delivery of a ship, a specialized team assumes responsibility for taking care of it so decisions can be made rapidly.
For the entire project life cycle, DNV GL will support the customer as a consulting partner. This close collaboration clearly paid off in the Liebherr and SAL transport project. “The cargo was overhanging the side of the ship. This is of great concern on certain sea routes so we had to file for a special permit,” recounts shipmaster Pfeiffer. The transport went smoothly, thanks to the excellent cooperation between SAL, Liebherr and DNV GL.
Meanwhile, technology continues to progress in the energy sector. Liebherr has already begun building the next LHM 800 crane, which will be installed at the container port in Montevideo, Uruguay. DNV GL will be on board again, true to the motto “Never change a winning team.”
Image below: Loss of cargo during loading or unloading is a worst-case scenario.
Source: DNV GL Maritime Impacts Magazine
The opinions expressed herein are the author's and not necessarily those of The Maritime Executive.