Marine Fire Protection: An Ungoverned Space
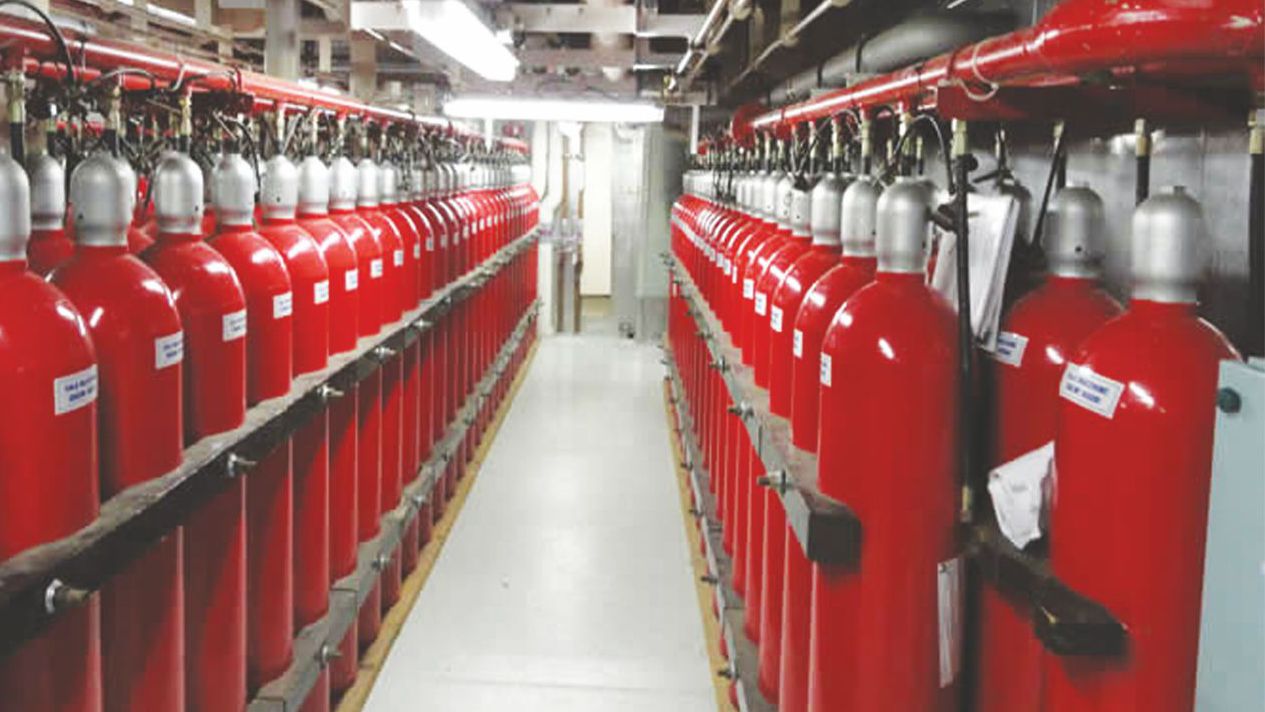
Fire protection remains an “ungoverned space” within the maritime industry. There are are too few qualified engineers who may be considered subject matter experts in marine fire engineering, and too often, marine fire protection is seen as a cost than an investment and something vital to the overall business activity of the customer. A “safety first” culture often remains both un-pursued and unrewarded.
In terms of ships extinguishing systems there exist two broad categories: sprinkler systems and gas systems. The former can suffer leakage, but the latter can cause catastrophic effect given its physical pressures. Overall, the value of the marine assets that fire systems protect is increasing rapidly but the competitive nature of the free market in the fire and marine industry places great pressure on it to deliver systems which often only minimally comply with the regulations and deliver the asset protection at the most economical cost.
Our experiences in the shipping industry globally have included wonderful ones of professionalism and care from dedicated former chief engineers, master mariners and fleet managers. Over 25 years we have received technical advice from some of the leaders in the industry both in the UK and the USA but also from Canada, Australia, Germany, Hong Kong, Denmark, Norway and Singapore. Trade and certification organizations such as the Institute of Marine Engineers, Science & Technology, Fire Industry Association, International Marine Purchasing Association, Shipbuilders & Suppliers Association in the UK and the NFPA and UL in the USA have become a part of our fabric.
Set alongside these positive developments, however, are anecdotal experiences which are highly concerning:
- Systems portrayed and installed by contractors as NOVEC 1230 fire protection fluid but filled with sand or water.
- High pressure gas systems without the means to actuate them.
- Bathroom weighing scales being chained to the CO2 cylinders in an effort to comply with IMO SOLAS FSS Code regulations.
- Cheap cylinder pressure gauges sticking in position under humidity or mechanical fatigue.
- Safety pins being retained in position in the cylinder valves after installation.
- Marine CO2 systems with an estimated 20% of the CO2 cylinders installed on commercial shipping being empty or partially-filled.
- Over-filled and under-filled cylinders.
- Pipework and cylinders freshly painted but with severe internal corrosion leading to particulates of rust which block the discharge nozzle mechanism.
- Room integrity testing with questionable results and with the room integrity remaining un-monitored after testing.
- Liquefied gas extinguishants being confused by installers and customers with Inert gas systems.
- A lack of understanding of the organic compounds of some liquid extinguishants and their corrosive effect on the cylinder in the event of condensate ingress.
- Shipping companies not implementing the FSS code of the IMO SOLAS regulations.
Our Safesite™ and Safeship™ concepts aim to deliver technologies which enhance safety at customer critical infrastructure at sea and on land, putting safety first.
Accidents
In aerospace, if a fault occurs on an aircraft that information is quickly and openly shared with airline operators, civil aviation authorities and engineering organizations. In contrast, in shipping, unless a fatality occurs it is left un-reported. The number of ships with partially-filled, over-filled or empty cylinders and the number of accidental discharges or slow seepages are occurring are left un-shared and unknown. Serious accidents involving fire protection equipment do occur:
September 2004 – Hong Kong - A routine inspection of the fixed CO2 fire extinguishing system led to the death of four officers (HKSAR, n.d.)
November 2008 - Akula II K-152 Nerpa - At least 20 people died on a Russian nuclear submarine when a Halon fire extinguishing system was activated by mistake (BBC News, 2008 and Red Banner Northern Fleet, 2008).
May 2010 – The uncontrolled release of fire-extinguishing gas into engine room of the Marsol Pride, at Tui oil and gas field (TAIC, 2011)
August 2011 - Accidental discharge of carbon dioxide on board SD Nimble, resulting in serious injury to a shore-based service engineer at Naval Base Faslane (MAIB, 2011)
July 2014 - Port Hedland, Western Australia – A fire started in the engine room of the bulk carrier Marigold. Firefighting by the ship’s crew included activating the Halon gas fixed fire suppression system for the engine room. However, a full release of Halon gas did not occur, nor was the engine room effectively sealed. (Safety4Sea, 2016)
February 2015 – Twenty-nine Palms, California - 22 U.S. Marines injured when a Halon-filled fire extinguisher went off (Bustle, 2015)
Marine Servicing
Marine servicing companies bid to service a ships CO2 system; this can comprise two hundred to six hundred 45 kilogram CO2 cylinders per ship. These are under 720 psi/ 49 bar of pressure. They can discharge accidentally or be subject to slow seepage. Some marine service companies estimate that at one time 20% of a ships CO2 cylinders have discharged or partially leaked their contents and there are over 55,000 commercial vessels at sea at any time.
Servicing is often done at sea, and the ship may only be available to the contractor for four hours; the winning contractor is often the one who bids lowest. Historically, and as only one component of a CO2 system inspection, these marine service crews shut down the CO2 system, dismantle it and weigh each cylinder.
On average each cylinder will take 40 minutes to dismantle, weigh, record and re-install, meaning that it would take 400 man-hours to achieve that on a 600 cylinder marine installation.
Using a type-approved ultrasonic liquid level indicator, a perfect condition cylinder can be checked for contents in 30 seconds; the average time to record and validate readings should take 1-3 minutes per properly-filled cylinder. This still equates to 10 to 30 perfect man-hours for this task alone. Too many times, therefore, good marine servicing companies may not have the minimum amount of time required to perform the inspection.
However, there are other companies who are said to randomly check some cylinders and then place “tested stickers” on the rest. Testing is important: because the normal design concentration of CO2 of 34-72 v/v % is above the nearly immediate acute lethality level, an extremely narrow safety margin exists for these systems.
Given the risk and the difficulties of manual inspection, it seems unfathomable then that these systems are not permanently monitored rather than leaving them to stand alone unsupervised 364 days a year until their annual certification.
UK Technology
High value shipping assets are critical infrastructure to the global economy with widespread effects in the event of their downtime or shutdown. Their asset values requiring fire protection far exceed the delivery of minimal compliance and the cost or damage to reputation far in excess of the cost of a real-time monitoring system.
Technologies exist right now that can mathematically and far more efficiently test room integrity. They exist to quickly, momentarily and highly accurately identify pipework corrosion. Gases under pressure can be monitored and liquefied gases can be permanently monitored. Contents and pressure can be simultaneously monitored offering remote diagnostics and remote monitoring capabilities and can extend to the delivery of autonomous systems in relation to them.
Technologies are soon to exist to monitor both liquid content and gas pressure of a cylinder safely – from the external sides of the cylinder rather than within it – in both fixed and portable forms. If we can monitor the contents we can calculate the mass/weight of the liquefied extinguishant.
These technologies offer great opportunity to the industry. They enable customers to have confidence that a fire company has installed a gaseous extinguishing system with a semi-autonomous monitoring capability to safeguard it. What CEO of a shipping company today wants to be shown to have installed a fire system that is left standing and unsupervised over thousands of miles of open seas and often in extreme weather states until its annual certification check?
This is presently an “ungoverned space” in the maritime sector. As the world changes, so must our industry integrate technological solutions to provide a bulwark against minimal - and even occasionally flagrant - disregard to the application of standards and good engineering practices.
About the Author
Carl Stephen Patrick Hunter is CEO and managing director of Coltraco Ultrasonics, a designer and manufacturer of portable instruments and fixed monitoring systems for the naval, shipping, offshore, energy and fire industries.
He is an honorary doctor of science, fellow of the Institute of Marine Engineers and member of the Royal Aeronautical Society, the Royal Institution of Naval Architects, Royal Institute for International Affairs, Royal Society of Asian Affairs and Royal United Services Institute. Dr. Hunter is also a member of the Export Council of the Fire Industry Association and Working Group Gases.
The opinions expressed herein are the author's and not necessarily those of The Maritime Executive.