Pilot Hole Drilled Using New Riserless Technology
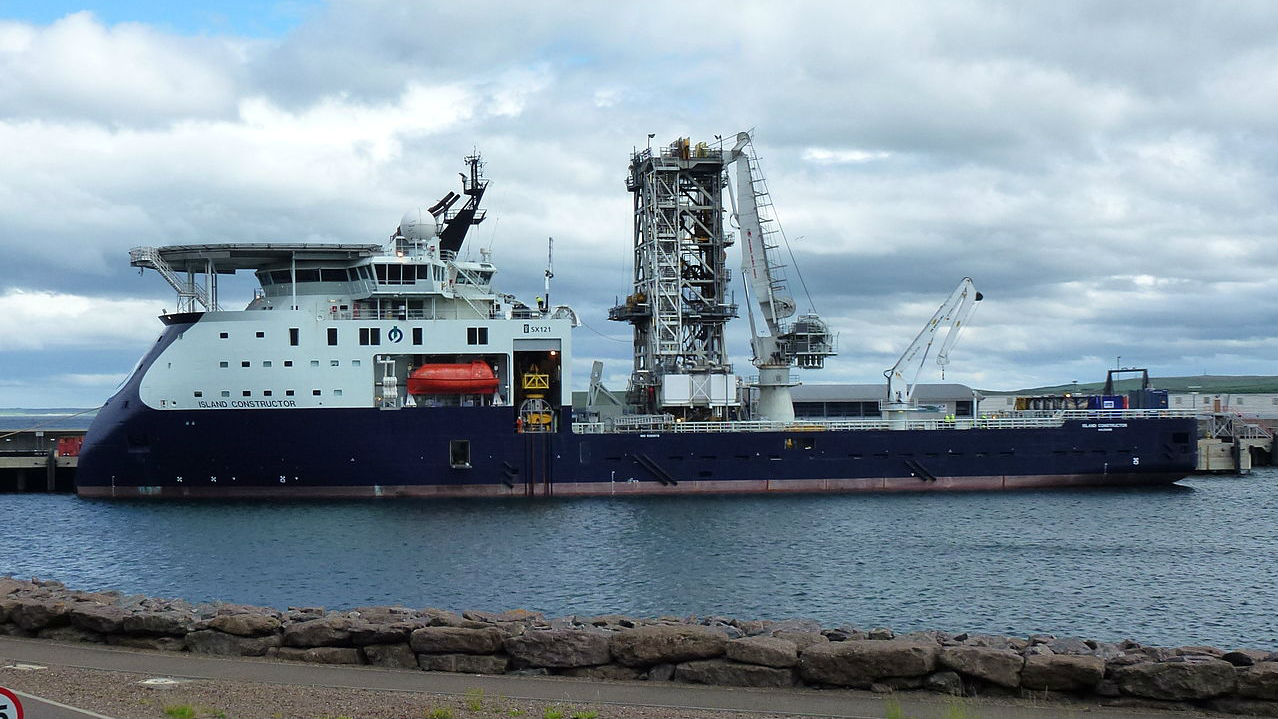
Island Offshore has successfully drilled a pilot hole for Centrica Energy by means of open water coil tubing. This technology has never been used in the offshore industry before and proves to be a safer and cheaper alternative to traditional drilling using a rig, says the company.
The offshore construction vessel Island Constructor was given the assignment to drill a shallow gas pilot hole down to 360 meters below mud line at the Butch PL 405-field, north of Ekofisk, to log for gas, and plug the pilot hole with cement if gas was discovered. Pilot holes are drilled to reveal shallow gas in the formations in advance of the actual drilling of the production wells. Shallow gas can be described as hidden gas pockets encountered at a depth close to the surface or mudline which can lead to blowout in the early stages of drilling.
“To use a rig for pilot hole drilling is much more costly than using a mobile offshore unit like the Island Constructor,” says Anders Olsen, Project Manager in Island Offshore. “Should one come across gas and the hole needs to be plugged, it will imply large costs to move the rig to a new location for a possible new pilot hole. The risk involved with using a rig compared to a vessel is also considerable as it will need far more time to move away should a blowout occur.
“In addition the coil tube’s flexibility makes the vessel able to keep pumping mud down the well to stop a potential shallow gas blowout, while moving to a secure area,” says Olsen.
Instead of using a marine riser, the coil tube is kept in tension between the vessel and the subsea injector by means of a second injector installed on board. The actual tube does not rotate, only pressurized fluid inside the coil activates a hydraulic motor which makes the bit rotate. The subsea injector pushes and pulls the coil tube in and out of the well.
“We have aimed for this since 2009. With coil tubing one can perform heavy maintenance to increase production and squeeze more oil and gas out of the wells,” says Department Manager Top hole drilling in Island Offshore, Per Buset.
Today these operations are performed by using a marine riser from a rig, which one can feed the coil tube down into. This is both expensive and time-consuming.
Island Offshore owns and operates three light well intervention vessels in the North Sea. Traditionally these vessels run wireline down the wells. One can perform some maintenance with wireline technology today, but with coil tubing one can do considerably more. Pumping fluid down the well and perform heavier maintenance such as scale removal in the production tubing to achieve original dimension of the tube is one example.
Last year this innovative technology was applied for the very first time in a totally different setting: It was used to drill core samples for what is to be the longest and deepest subsea road tunnel in the world, named Rogfast. The contracting company was the Norwegian Public Road Administration.
“We are now taking the next step with coil tubing. To apply this technology in pilot hole drilling is pioneering. This is a challenging and exciting project which receives great attention with our customer and the industry in general. In addition to be significantly safer and cheaper than using drilling rigs, emissions to the environment are also reduced with 50 percent compared to conventional drilling,” says Olsen.
“After finishing the Rogfast-project with great success our technology was now qualified, and the oil companies started realizing that the same technology could be used to drill the topmost part of a well to log for shallow gas. Centrica Energy took the plunge and became the first company in the world to use this kind of technology for offshore purposes,” says Buset.
The operation was planned to last for seven days on the field, but it was finished in just over four days without finding shallow gas. With that the drilling rig could start drilling the production wells and be sure that it is gas free.
“Moving a rig and other equipment on the seabed due to shallow gas are very costly; several hundred million NOK in a worst case scenario. By using our alternative method Centrica has, according to their calculations, saved roughly 30-50 percent compared to using a rig. In addition the risk level is dramatically reduced,” Buset continues.
Island Offshore is the developer and the owner of the technology which is integrated with Baker Hughes’ topside equipment. The aim is to use the same principle within light well intervention, plug and abandonment as well as other types of well intervention.
In August this Year Island Offshore received a technology award for this exact technology during the Deepwater Intervention Forum in Galveston, Texas.