Wind Blows Change for Project Cargoes

Graig Ship Management shows why there is more to getting “green” than most people will ever know. The heavy lift project cargo game just got a little harder.
Go back just fifteen years and most people thought that large-scale electricity generation from wind turbines was just a lot of hot air. Since then, a wind of change has blown through energy thinking. The U.S. government has come out in favor of wind turbines, and windier states such as Texas have moved to embrace wind power. Today, the U.S. claims to be home to the world’s largest demand for wind turbine power, a claim which might be contested by energy-hungry Europe, India and China, all areas where huge wind farm projects, both on and offshore, are under development.
• Heavy Lift Thinking Shifts Direction, Too
“Wind turbines are big, awkward things to transport, and they are also not easy to manufacture,” says Ian Morgan, CEO of Cardiff-based Graig Ship Management (GSM). “So the explosive growth in demand for wind farms is creating demand for project cargo shipment to move wind turbines from manufacturer to site. And it is also creating demand for new types of ships to move the turbine parts efficiently and to install them, as the offshore sites need to have specialized installation vessels and, in the future, the turbines on site will need a lot of maintenance support. The other wind of change is that turbine parts move one way, freeing up project cargo ships to move goods on the back haul, which has changed the global market for project cargo.”
GSM has a track record in this area, having built and operated 19 specialized heavy lift project cargo vessels in China in the 1990s, and has since then managed a fleet of project cargo ships. “Today, we manage ten ships with project cargo capability, and in 2001 we oversaw the building of the Mayflower, the first-ever specialized wind power installation vessel,” says Morgan. “Today we are helping SE Shipping of Singapore to build four very specialized heavy lift wind turbine transportation vessels in China. They will work on long-term contracts for Suzlon Energy, the world’s fifth largest turbine manufacturer. Suzlon has manufacturing plants in India, China and the U.S. and is supplying turbines to almost everywhere in the world. These new vessels, all for 2010 delivery, will transport them efficiently from the plant to a port near the site. And then the ships will be active in the market for other project cargoes as they reposition.”
SE Shipping, an independent Singapore-based specialized project cargo company, says the new vessels will be serving Suzlon Energy contracts on a variety of routes. The turbine voyages will typically be light, as the big components are the blades, around 50 meters long, but weighing less than 20 tons. The turbine towers are much heavier, but as they are 100 meters tall when built they are shipped in sections. SE says it has specified heavy cranes for the design so it can expand out of the wind turbine business, where it began, and offer project cargo shipment to the oil and gas industry.
• New Customer Requirements = New Challenges for GSM
The advent of wind power is not the only change factor in the project cargo market. “We see a trend towards much larger units,” explains Morgan. “Manufacturers want to build and assemble as much as possible at their own plant and keep local assembly to a minimum. So where twenty years ago lifts were smaller and lifts of 400 tons were rare, today we are quite often asked to move units over 40 meters long and weighing up to 400 tons. And we usually have to move them from a factory at a small port to a wharf somewhere close to the site. That calls for rather special ships and, above all, special, experienced crews.”
The ships being built for SE Shipping were designed by Norwegian consultants Polarkonsult AS. Managing Director Sigmund Sorensen says, “We designed these ships especially for SE Shipping’s needs. The key factor for wind turbine transportation is the size of the unobstructed hold. In this PK-148 design we have put the accommodation forward and two cranes on one side of the vessel, and have two cargo holds with clear openings of 76.05 x 20.50 meters and 23.40 x 20.50/13.20 meters. The two cranes are 450-ton lifts each, giving the vessel a total capacity of 900 tons. But that is not for the wind turbines which, although big, are relatively light. They are there to give the ship a lot of options in the general project cargo market. We are seeing demand from a number of owners for such ships, and we have a similar design but with 1,000-ton cranes ready. They combine the space needs of wind turbine cargo with the lift capacity and flexibility which project cargo demands.”
Morgan says GSM is using its experience to supervise the building of the vessels at China’s Wenzhou Zhongou Shipbuilding Co. Ltd. “These are very good designs,” he says, “with a lot of modern thinking. Our role is to make sure they are built to the highest standards. That means a lot more NDT (non-destructive) testing and special attention to critical areas such as the crane pedestals, for example. But we must not lose sight of the fact that for project cargo work, while the right ship is important, the right crew is even more vital. That’s one particular thing I like in this Polarkonsult design: There is accommodation for 26 crew. We only have room for 13 or 14 on our Confidence-class vessels. That is plenty to operate the ship safely, but we need more room to carry trainees and cadets. We have to preserve the skill base, and there is no way moving project cargoes can be learned from a book. It has to be learned through experience.”
Experienced project cargo masters are amongst the highest paid seafarers today, reflecting their relative scarcity. “When we are handling large cargo units, everyone bar the cook is turned to,” says Morgan. “The A/Bs drive the cranes, the mates and master are supervising, the engineers are on top of ballast transfer and power demand. It is a huge teamwork business, dependent on calm, experienced planning and communication.”
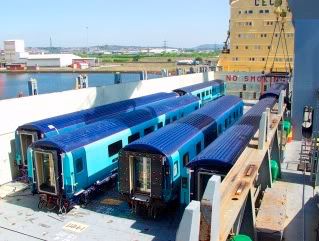
Examples of recent interesting project cargoes carried by GSM include a 48 meters-long demethanizer tower shipped from Porto Marghera in Italy to the Middle East on board the M/V Fanja. The 230-ton lift was well within the capability of the ship’s twin 200-ton cranes, but the length was a challenge as the distance between the cranes is only 40 meters. The Fanja is one of the 9,000-dwt., Confidence-class vessels built in China in 2000 for Graig and today owned by Oman Shipping and managed by GSM. Another interesting example was loading the fuselage parts of an Airbus onto the M/V Hamra, another Confidence-class vessel, for shipment from Germany to France. The section weights were up to 110 tons, but large and bulky to handle.
Unusually, perhaps, in today’s world of shipping, project cargoes offer ships’ crews an interesting and challenging life. “Typically they have to load at out-of-the-way places, not a normal port, and there is huge variety and also satisfaction in getting each lift right,” says Morgan. “We have a pool of experienced masters and officers and a retention rate of over 80 percent. They really enjoy the challenge of the job. We are looking at new projects constantly and, with the changing patterns of demand in project cargo, we believe the special expertise is a value-added factor. We have a lot of cadets from the UK, Philippines, and Vietnam, and they will be the core expertise on which we will continue to develop the business.”
In the fast-changing and demanding world of project cargo management, no challenge would seem to be too daunting. – MarEx